Report or suffer the consequences: How transparency in the process industry is opening the door to efficiency gains
By Jeroen Coussement, CEO and co-founder of Ghent-based scale-up Factry
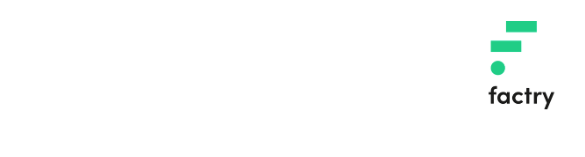.png)
Developments in the process industry in 2025 will be marked not only by technology, but also by reporting, transparency and, as usual, the relentless quest for bigger margins and efficiency. Companies that jump on the bandwagon will not only take a big step towards compliance but, in their drive for innovation and digitalisation, will also open the gate for competitive advantage and employee engagement in the workplace. Thus, more than ever, data transparency and accessibility become the keys to success.
The process industry is going through profound changes. Among others, laws and regulations such as the Corporate Sustainability Reporting Directive or CSRD, which will come into play in January 2025 as part of the Green Deal, force industrial players to report transparently on their CO2 emissions and environmental impact. Ensuring food safety is another key driver for this transparency. While these companies used to focus mainly on the highest possible output from a business perspective, the entire production process will now have to be mapped out.
This evolution, spurred by increasing social and political pressure, is forcing industrial companies more than ever to understand the data generated in their production environment. This remains a challenge for many as data has long been collected, but often on paper or in closed systems, making analysis difficult. Many now need to revisit that architecture to report transparently on their operational data.
For those who seize this opportunity, more transparency opens doors to not only compliance, but also to optimised operations. For example, those who have to report on energy consumption can immediately start using that knowledge to reduce that consumption and increase efficiency. In addition, more transparency offers perspective to customer relations, as they too increasingly expect traceability of the origins, ingredients and processes behind the products they purchase. However, anyone who puts compliance lower on the agenda will be too late. Regulations are only getting stricter and competition is getting tougher by the day.
Open by default
Besides regulation, democratising or making data accessible will also become increasingly important. While production or process data used to be the exclusive domain of technical profiles, within many organisations the expectation is growing that just about everyone should have access to that information. Employees, even those without a technical background, now want access to relevant data to make informed decisions or predictions, just as they are used to in their private lives.
This trend is not just technical, but also involves a cultural shift. By giving workers access to production floor data, you nurture a sense of ownership. This access not only leads to more efficiency, but also to innovation and empowerment. Whoever is behind the wheel, needs to feel involved.
Although some companies are still hesitant about an open data culture, an ‘open by default’ approach is increasingly becoming the norm. This openness promotes collaboration and innovation in all layers of the organisation, which is decisive in times of increasing competition and cost pressure. Informed employees can act proactively and contribute to process improvements. At the same time, this trend requires a change in mindset and infrastructure. Companies still clinging to limited data access will find that they’ll be missing out on opportunities in terms of innovation and efficiency.
Integration of external factors
A third trend is the integration of external factors into automation processes. Whereas traditional control loops merely factor in internal production and process data, external indicators such as weather forecasts, energy prices and consumption and raw materials will increasingly be factored in. This offers unseen opportunities for optimisation. Compare it to the heating at your home. A standard thermostat controls the temperature purely based on set values. However, if you add advanced parameters such as expected sunshine, you can adjust the heating much more precisely and thus save on your bill. We now see the same principle permeating the process industry.
This trend is further reinforced by technological advances and external market pressures, such as high energy prices and quality expectations. Companies that manage to integrate these external variables effectively can not only save costs, but also operate more sustainably and flexibly.
The pieces are moving
Although Industry 4.0 has been talked about for years, the vast majority of companies are only just getting to the basics of digitalisation. The pieces are finally moving and we see companies taking serious steps in their journey towards further digitalisation. But we need to watch out for a new hype cycle around ‘Industry 5.0’ when many companies have not yet come to grips with Industry 4.0.
The current shaky economic and geopolitical climate puts the importance of digitalisation into sharp focus. In Europe, the need to keep production local and sustainable is high, and digitalisation is an important lever to ensure efficiency and better margins. Therefore, innovation should not be limited to a small department, but should permeate the entire organisation. Digitalisation and accessible data are no longer nice-to-haves, but absolute necessities to stay relevant in an increasingly demanding market. Digitalisation is not just a technical issue, it is a culture change that drives innovation at all levels of the organisation.
Companies that understand and embrace this will be the leaders of tomorrow.
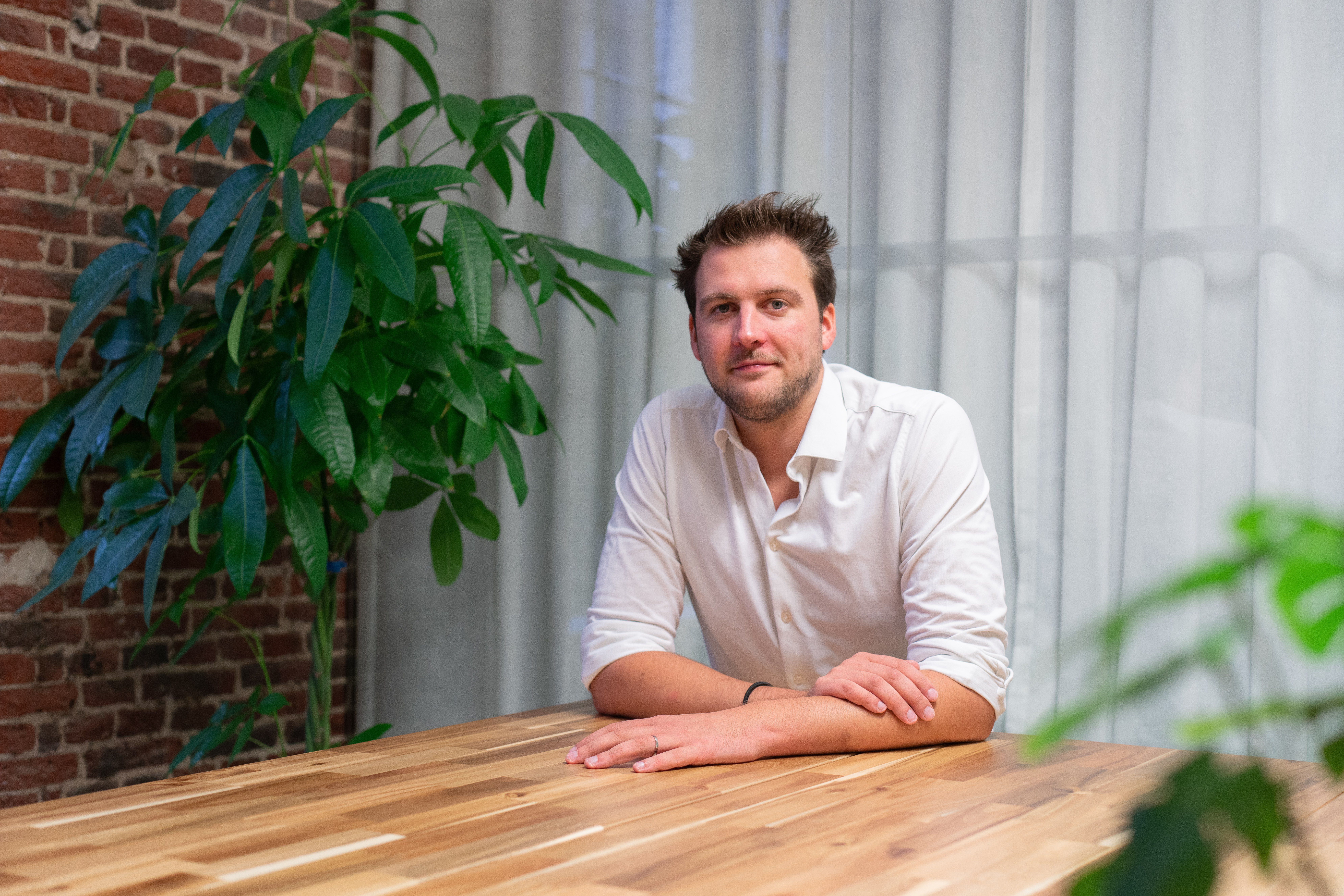